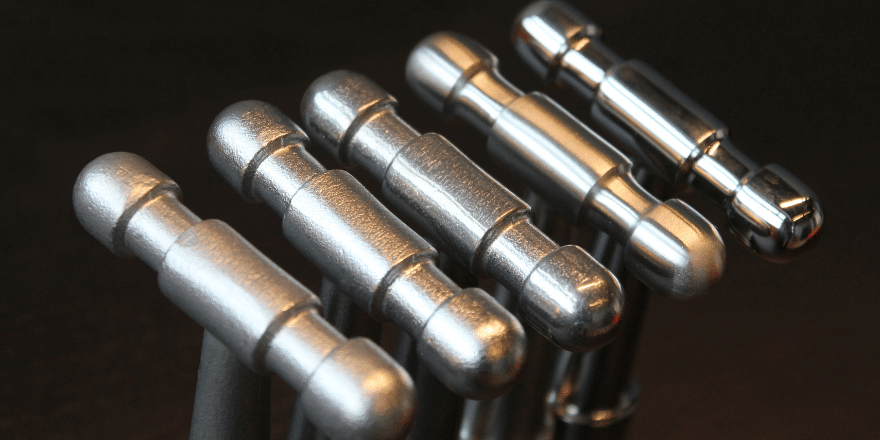
HOW TO CHOOSE THE RIGHT FINISH FOR ALUMINIUM PARTS
In the production of aluminium parts, the finish plays a significant role in the quality and lifespan of the final product. But how do you determine which finish or surface treatment is best for your project? ELCEE supports buyers and engineers every day in making the right finishing choices for high-quality aluminium castings. In this blog, we discuss what to consider when determining the appropriate finish or surface treatment.
WHAT IS THE PURPOSE OF THE FINISH?
Before selecting a specific finish, it’s essential to establish its purpose. There are three main reasons for finishing cast aluminium parts:
- Protection – against corrosion, wear, or chemical influences.
- Aesthetics – for a high-quality or uniform appearance.
- Functionality – such as conductivity, adhesion of coatings, and enhancement of mechanical properties.
In aluminium die casting within the electrical engineering field, a conductive finish may be required, while in other cases, the emphasis is on corrosion resistance or visual uniformity.
THE CASTING PROCESS AFFECTS THE FINISH
Components can be produced in aluminium using various casting techniques. Each technique has a different process and therefore results in a component with distinct specifications. The surface quality is significantly influenced by the casting technique used.
- The suitability of specific finishes for this surface depends on the casting technique employed. Sand casting and gravity die casting often result in a rough surface that must first be mechanically treated before the final finish can be applied.
- Aluminium die casting (high-pressure die casting) produces a smoother surface but may contain micro-defects that can affect the adhesion of coatings or anodisation.
From the outset of designing and engineering the component, the desired product specifications of the final result should be considered, ensuring that the casting process and desired finish align properly.
CHOICE OF FINISHING TECHNIQUE
There are several finishing options available for aluminium parts, each with its own specifications:
- Anodising – creates a hard, wear-resistant oxide layer with decorative possibilities.
- Powder coating – provides a strong, durable colour layer in various finishes.
- Chromating – suitable as a corrosion-resistant intermediate layer or for electrical applications.
- Polishing or brushing – results in an attractive finish or prepares the surface for other treatments.
CONSIDER TOLERANCES AND DIMENSIONING
Finishes and can affect the dimensions of a part. Especially with products that have tight tolerances, it is crucial to consider thicknesses and surface treatments during the design phase. We assist you in optimising the design so that the final product meets all functional and dimensional requirements after finishing.
EARLY COLLABORATION FOR COST-EFFECTIVE PRODUCTION
ELCEE has extensive experience with both the casting process and finishing of aluminium casting parts. By involving us early in the process, we can advise on material selection, tolerances, and the most suitable finishing techniques. This helps prevent surprises in later production phases and ensures efficient, cost-effective manufacturing.
ADVICE ON ALUMINIUM CASTING FINISHES
Choosing the right finish for aluminium parts is more than just an aesthetic choice; it is a critical component of the engineering and procurement process. By considering the desired function, the casting process, and technical requirements, you can work with an experienced partner like ELCEE to realise the optimal solution.
Get in touch
Need tailored advice on finishing your aluminium castings? Get in touch with us. Our engineers and product specialists are here to help.